The general purpose of conduit, or duct, is to provide a clear, protected pathway for a cable, or for
smaller conduits, sometimes called inner ducts. Advances in cable technologies, as well as the
expense of repairing sensitive cable materials like fiber optic cable, have driven preferences for
protective conduit over that of direct burial. Polyethylene (PE) conduit provides mechanical
protection to fragile cable materials like fiber optic and coaxial cables, as well as protection from
moisture or chemicals and even, in some cases, animals. Furthermore, the permanent pathway
provided by conduit also facilitates replacement projects or future installations of additional cable or
duct. Originally, PVC was utilized, but ultimately, PE has emerged as the material of choice due to its
distinct advantages in installation options, versatility and toughness.
High density Polyethylene (HDPE) conduit had been the material of choice to protect the fiber optic
highways for decades.
Advantages of PE Conduit
High Density Polyethylene (PE) is the most commonly used PE material for conduit. PE conduit
delivers significant physical property advantages over other conduit materials:
• Ductility – tough, PE conduit will better resist brittleness with age or cold weather.
• Low temperature impact resistance – PE withstands low temperature impact better than any other material. This is illustrated by impact testing on PE conduit conditioned at -15°C as compared to other materials conditioned at 22°C.
• Permanent flexibility – PE conduit bends and flexes without breakage, even with ground heaves or shifts, over a wide range of temperatures.
• Temperature versatility – PE conduit can be installed over an ambient temperature range of 0°C to 80°C. Power conductors rated at 90ºC and medium voltage cable rated at 105ºC are permitted for use with PE Conduit.
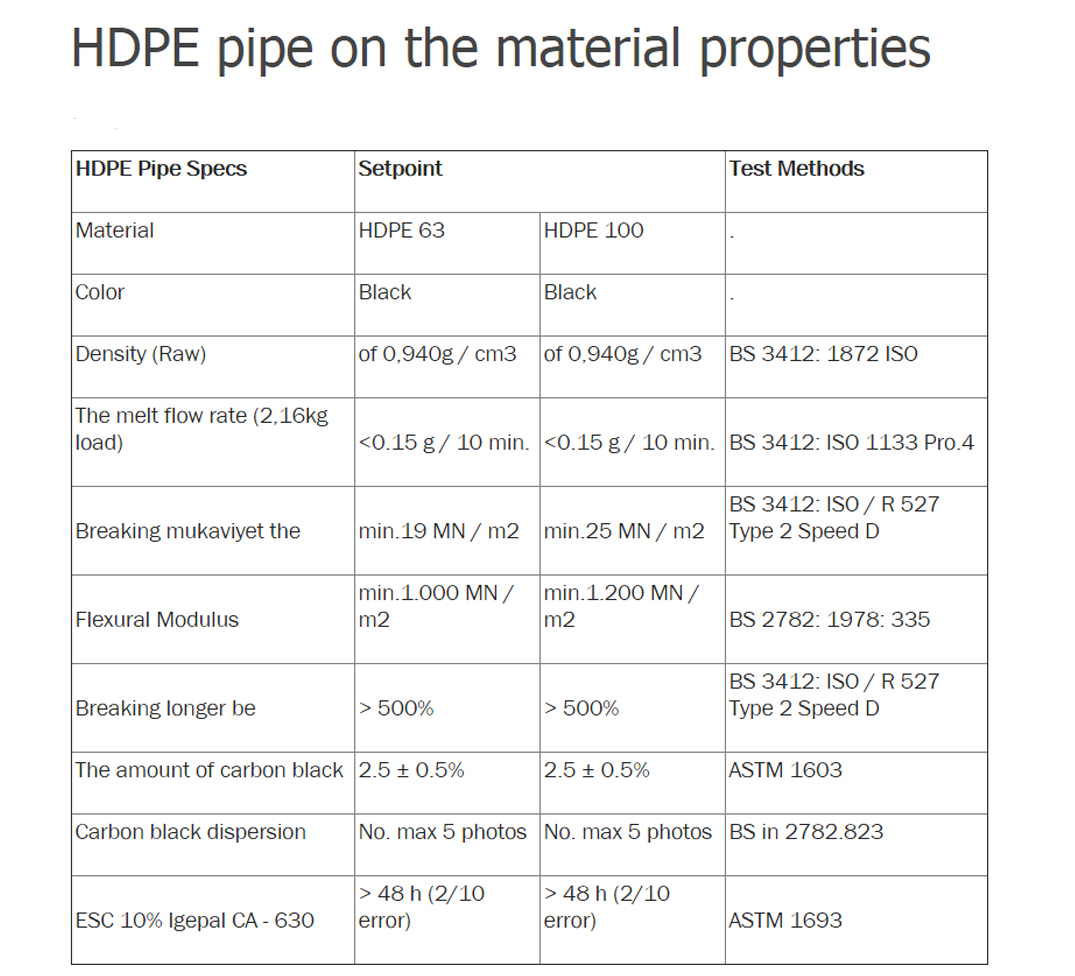
